Металлургия является одним из самых больших потребителей первичных энергоносителей в украинской промышленности. Если в развитых европейских странах на производство одной тонны чугуна расходуется около 450 кг условного топлива, то в Украине –650 кг. Не говоря уже о выпуске проката, где отечественные нормы практически вдвое выше западных. Пути сокращения энергозатрат давно известны и апробированы: в первую очередь – это замена мартеновского способа выплавки стали на кислородно-конвертерный. К сожалению, в Украине до сих пор около половины (46%) всей стали получают мартеновским способом.
Почему конвертеры
Лидирующие позиции среди известных способов массового производства стали кислородно-конвертерный процесс занимает благодаря отсутствию затрат топлива. Здесь для получения стали используется не дефицитный в Украине природный газ, а кислород, получаемый из воздуха, пропущенного через специальный разделительный блок.
Впервые в мировой практике кислород для продувки чугуна был применен советским инженером Н.И. Мозговым на киевском машиностроительном заводе `Большевик` в 1933 году. В промышленном масштабе кислородно-конвертерный процесс впервые был опробован в Австрии в 1952 году. А в СССР первый кислородно-конвертерный цех (ККЦ) был введен в эксплуатацию в Днепропетровске на металлургическом заводе им. Петровского в 1956 году.
С тех пор кислородно-конвертерный способ получения стали стал ведущим, постепенно вытеснив ранее лидирующий мартеновский. Сегодня данный способ обеспечивает большую часть мирового производства стали. И не удивительно, ведь его технико-экономические преимущества налицо. Среди них – более высокая производительность на единицу выплавляемой стали, меньшие капитальные затраты, более благоприятные условия для механизации и автоматизации производственных процессов и совмещения процесса выплавки стали с ее непрерывной разливкой. При этом, кислородно-конвертерным способом можно переработать чугун практически любого состава и получать широкий сортамент сталей, включая легированные.
Что имеем
В Украине в настоящее время действует семь кислородно-конвертерных цехов (металлургические комбинаты `Arcelor Mittal Кривой Рог`, `Азовсталь` `ММК им. Ильича`, `ДМК им. Дзержинского` и `ДМЗ им. Петровского`, Енакиевский и Алчевский металлургические заводы). В них насчитывается 21 конвертер, с помощью которых получают чуть более половины всей украинской стали. Однако до полной замены мартенов конвертерами еще далеко. А ведь снижение доли мартеновского производства хотя бы до 15% позволит экономить около 1,45 млрд. куб. м газа в год.
Сегодня ключевые позиции по производству стали кислородно-конвертерным способом занимают меткомбинаты `Arcelor Mittal Кривой Рог` и `Азовсталь`. На Криворожском комбинате первый конвертер емкостью 35 тонн был введен в эксплуатацию еще в 1957 году, одним из первых в нашей стране. Сегодня же производственная мощность конвертерного цеха предприятия достигает 5,4 млн. т стали в год. В состав цеха входят шесть 160-тонных конвертеров (2 блока по 3 конвертера).
Около двух лет назад на предприятии был принят инвестиционный план по модернизации комбината, который предполагал строительство нового конвертерного цеха с двумя конвертерами общей производительностью 5,2 млн. т в год. Реализация проекта позволила бы вывести из эксплуатации устаревшие мартеновские печи и ДСПА суммарной производительностью около 2 млн. т в год. Однако из-за кризиса реализация его была приостановлена, сегодня проект находится в режиме ожидания.
Крупнейшие в стране конвертеры функционируют на `Азовстали`. В кислородно-конвертерном цеху, введенном в эксплуатацию в 1977 году, сегодня работает два конвертера по 330 тонн, годовой номинальный объем производства составляет 4,5 млн. т. Разработанной несколькими годами ранее программой модернизации завода была предусмотрена полная реконструкция конвертерного цеха и строительство третьего конвертера. Реализация проекта помогла бы увеличить мощности предприятия по стали до 8 млн. т в год и закрыть существующее мартеновское производство производительностью до 2 млн. т в год.
До настоящего времени в рамках данной программы успели осуществить лишь капитальный ремонт конвертера № 1 с заменой корпуса (инвестиции в проект составили свыше 20 млн. грн.). Ремонт второго конвертера и строительство третьего отложены `до лучших времен`.
Неосуществленные проекты
До кризиса программы модернизации, включавшие, в частности, строительство конверторных цехов с полным выведением из производства мартеновских печей, были разработаны и на других меткомбинатах страны.
Так, на ММК им. Ильича был проработан проект реконструкции сталеплавильного производства с целью замены устаревших мартеновских печей на конвертеры. Проектом предусматривалось строительство трех 160-тонных конвертеров мощностью порядка 1,2 млн. т каждый, которые должны были заменить мартены суммарной мощностью до 4 млн. т в год.
К настоящему времени, по словам начальника отдела автоматизированного электропривода, электроснабжения и АСУ ТП АОЗТ `Тяжпромавтоматика` Александра Петровича Данилина, который непосредственно участвовал в разработке и внедрении проекта реконструкции сталеплавильного производства комбината, два конвертера уже введены в эксплуатацию, работы по третьему из-за невозможности финансирования пока отложены. Однако руководство предприятия с уверенностью заявляет, что уже в этом году планируется возобновление работ по переходу на кислородно-конвертерное производство.
Разговоры о замене мартеновского метода на конвертерное велись также на Макеевском МЗ, где сталь выплавлялась исключительно мартеновским способом. Так, в рамках программы реконструкции СПК до 2011 года здесь планировалось построить новый конвертерный цех, что позволило бы вывести из эксплуатации действующее мартеновское производство. Мощность комплекса планировалась на уровне 5 млн. т в год. Однако реальные инвестиции были минимальными, их едва хватало на поддержание имевшегося технического уровня метзавода, что отодвинуло строительство ККЦ на неопределенный срок.
Лишь на Алчевском МК несмотря на кризис удалось воплотить запланированный переход от мартенов на кислородно-конвертерное производство.
Наглядный пример
Строительство ККЦ на Алчевском меткомбинате считается наиболее значимым инновационным проектом в Украине за последние несколько лет. Не удивительно, ведь последний сталеплавильный комплекс в нашей стране был построен более 25 лет назад.
На Алчевском МК строительство кислородно-конвертерного цеха началось еще в 2006 году. Проектом предусматривалось строительство двух конвертеров емкостью 300 тонн каждый с соответствующей инфраструктурой: отделение перелива и десульфурации чугуна, пролет перестановки шлаковых чаш, отделение перегрузки и взвешивания металлолома, участок подготовки, хранения и транспортировки сыпучих материалов, комплекс газоочистительных сооружений и кислородный цех. Общая производительность ККЦ составляет до 5,5 млн. т в год. Длительность плавки от выпуска до выпуска – 40 минут. Среднесуточная производительность (с учетом общего количества плавок в год и полного рабочего времени) при работе обоих конвертеров – 58 плавок. Поставщиком оборудования и технологий для нового цеха выступила австрийская фирма Siemens-VAI, генеральной проектной организацией – НИИ `Гипросталь` НТЦ `Энергосталь`, генподрядчиком строительно-монтажных работ – ООО ПСП `Азовинтэкс`.
Строительство осуществлялось рекордно быстрыми темпами и не имело мировых аналогов. Уже в конце 2007 года был введен в эксплуатацию первый конвертер мощностью 3 млн. т в год. В 2008 году комбинат закончил строительство второй очереди и запустил второй конвертер.
Сегодня в состав ККЦ кроме конвертеров входят двухпозиционный агрегат печь-ковш, вакууматор камерного типа и две двухручьевые слябовые МНЛЗ номинальной мощностью 2,5 млн. т в год каждая, запущенные в 2005 и 2006 годах соответственно. В целом переход на ККЦ длился около 5 лет и стоил `Индустриальному Союзу Донбасса` более $1 млрд.
Жизненная необходимость
В настоящее время исключительно мартеновским производством, помимо Макеевского МЗ, располагают `Запорожсталь`, Донецкий МЗ и `Интерпайп Нижнеднепровский ТПЗ`.
При этом, безусловным лидером мартеновского производства в стране остается запорожский меткомбинат, что значительно подрывает его конкурентоспособность, так как себестоимость выплавки стали в мартенах на 10-15% выше конвертерной из-за большой энерго- и ресурсозатратности, а также значительных потерь продукции при производстве.
Интересно, что предприятие начало планировать переход на конвертерный способ производства стали еще в 2003-2004 годах. А в 2008 году был подписан контракт с Siemens-VAI о закупке оборудования для будущего ККЦ, который вступит в силу после первого поступления платежа с украинской стороны.
В целом данный инвестиционный проект `Запорожстали` предусматривает строительство двух конвертеров производительностью 250 тонн каждый, двух установок десульфурации чугуна, вакууматора и двух толстослябовых МНЛЗ. В новом цехе предполагается производство 4,7 млн. т стали в год. Производительность ККЦ рассчитана так, чтобы мощности доменного цеха использовались максимально: четырьмя печами будет выплавляться 4 млн. т чугуна в год.
По оценкам руководства комбината, переход на конвертерный метод позволил бы не только повысить производительность и снизить затратность производства, но и обеспечить выплавку стали с узкими пределами содержания элементов, улучшить качество поверхности проката, однородность структуры и свойств металла. Кроме того, предполагалось, что `Запорожсталь` после строительства ККЦ сможет заметно расширить марочный сортамент сталей, освоив выпуск, в частности, трубных марок, качественной конструкционной стали, стали повышенной прочности, стали для сосудов и котлов, работающих под давлением, а также стали для штамповки (в том числе, для автомобилестроения).
Реализация проекта также должна была дать предприятию возможность получать не только высококачественный горячий прокат, но и холоднокатаный лист, а также продукцию четвертого передела (ежегодно до 300 тыс. т `оцинковки` и листа с полимерным покрытием). Кроме того, предусматривалось снизить потери стали в обрези на 110 кг/т.
Но, несмотря на все преимущества кислородно-конвертерного производства с началом финансового кризиса руководство и собственники комбината в очередной раз заморозили строительство ККЦ. Это и понятно, ведь стоимость данного проекта, рассчитанного на длительный период реализации, может составить более $1 млрд.
В чем причина?
В настоящее время для решения самой насущной проблемы металлургической отрасли – ее энергозатратности и сильной энергозависимости украинскому горно-металлургическому комплексу необходима коренная модернизация, приоритетным направлением которой остается переход к конвертерному производству стали и полный отказ от мартенов. Однако практически все такие инвестиционные проекты, которые были начаты до кризиса, приостановлены из-за отсутствия средств.
В настоящее время действуют несколько видов льгот для промышленных предприятий, которые внедряют энергосберегающие технологии. Во-первых, это возможность беспошлинного ввоза энергоэффективного оборудования без уплаты НДС. По информации Национального агентства по эффективному использованию энергоресурсов (НАЭР), по состоянию на начало 2010 года этой льготой воспользовались более 50 предприятий разных отраслей и регионов. Во-вторых, для компаний, которые внедряют энергоэффективные технологии, существует возможность платить только половину налога на прибыль. Нормативная база для этого была оформлена еще в апреле 2008 года. Однако на сегодня этой преференцией пока не воспользовалось ни одно предприятие. В ближайшем будущем планируется принятие еще одного постановления, стимулирующего внедрение энергоэффективных технологий – возможность ускоренной амортизации ввезенного в Украину энергосберегающего оборудования.
Однако очевидно, что перечисленных мер пока недостаточно, и металлургические предприятия сегодня остро нуждаются в общей государственной программе стратегического развития. Именно ее реализация должна стать приоритетным направлением деятельности правительства в металлургии.
Ольга Фомина
http://www.rusmet.ru/
Трудности в переходе к современным технологиям выплавки стали в Украине
+380 44 237 XX XX +380 44 237 2567
Идентификатор: 8049
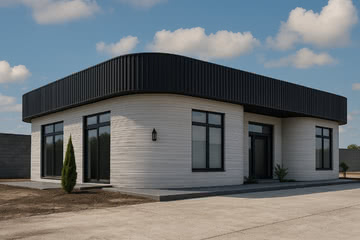
23 июн. 2025 г.